Labeling error recalls in CPG industry
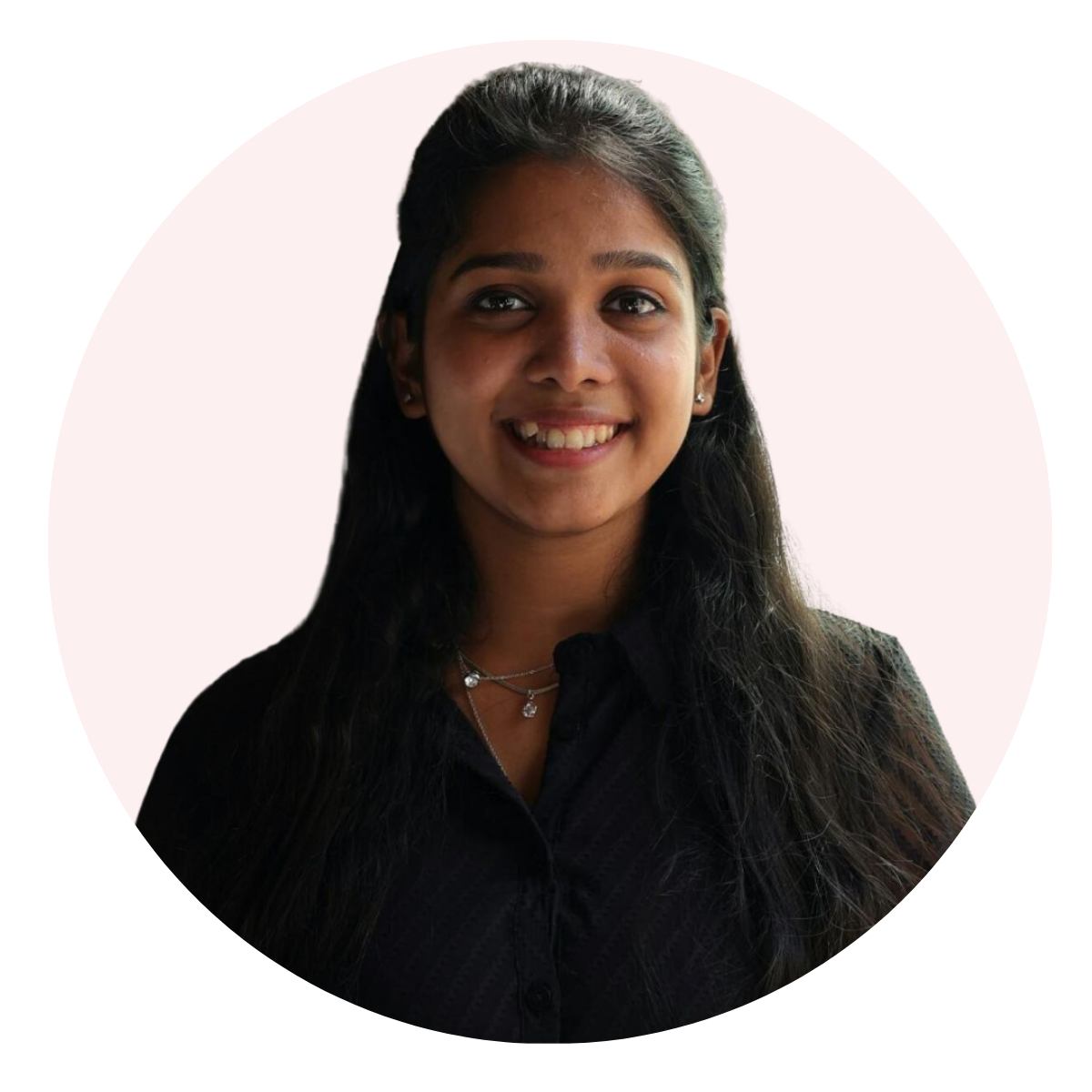
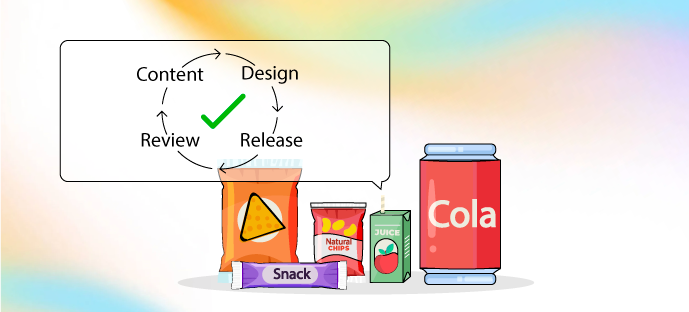
Launching a new product demands meticulous attention to detail to ensure compliance with regulatory standards and brand consistency. One of the common pitfalls in this process is manual errors and oversight during proofing of artworks, which can lead to inaccuracies in packaging labels. If left unnoticed, these mistakes can trigger product recalls, resulting in significant financial and regulatory setbacks.
Over time, product recalls have cost companies billions, damaged brand reputation, and reduced consumer trust. Particularly in industries like food and beverage and consumer packaged goods, where manufacturers operate on thin margins and high volumes, maintaining impeccable quality is important. During January 2024, the FDA issued recalls for 30 products, with 18 of these recalls being due to the presence of undeclared allergens or other ingredients.
As production rates surge to meet consumer demands and expectations, the risk of errors escalates. According to the FDA, a substantial portion of allergen-related recalls stem from bakery products, snacks, candies, dairy, and dressings, with milk, wheat, and soy being the most frequently recalled allergens. Green Valley Foods, a Devils Lake, ND establishment, is recalling approximately 4,062 pounds of frozen meat pizza products due to misbranding and undeclared allergens.
The presence of contaminants, whether foreign objects such as plastic or microbial agents like bacteria, poses a significant risk, often necessitating product recalls. Ensuring stringent quality control measures is essential to mitigate these threats effectively.
Incorrect or missing details on labels pose significant health hazards to consumers, often necessitating recalls. Checking your labels for the five FDA requirements is a critical part of quality control. Few crucial details, if overlooked, inevitably result in product recalls, including:
Packaging label errors can have serious consequences for both the consumer and the manufacturer. 3 potential packaging label errors that can turn your product:
Quality control lapses during manufacturing or packaging can lead to defective products reaching consumers, such as food spoilage due to insufficient package sealing. These failures compromise product safety and integrity, risking consumer health and brand reputation. Implementing robust quality control measures is imperative to prevent such issues and ensure consistently high product standards throughout the manufacturing and packaging processes.
During the creation phase, ManageArtworks copy manager acts as a central repository for label content, facilitating collaboration among departments responsible for providing essential information such as product details, ingredients, and marketing claims. By streamlining content approval processes, one can ensure that only accurate and approved information is incorporated into packaging artwork, minimizing the risk of errors from the outset.
In the review phase, ManageArtworks plays a pivotal role in orchestrating the review and approval process. It provides a structured framework for stakeholders across different departments to review artwork drafts, offer feedback, and approve revisions. By centralizing communication and version control, ManageArtworks ensures that all relevant parties are aligned and that the correct version of artwork progresses seamlessly to the next stage, thereby reducing the likelihood of oversight or miscommunication.
To aid proofreading, ManageArtworks offers a suite of tools designed to meticulously inspect artwork for accuracy and compliance. Features such as Copy Compare, Font analysis, Spell Check, Barcode Analysis, Annotation Tools, and Checklists enable thorough inspections of artwork elements. These tools help identify and rectify any discrepancies or errors, ensuring that the final artwork meets regulatory requirements, adheres to brand guidelines, and contains accurate information essential for consumer safety.
ManageArtworks' Adobe plugin tool facilitates designers to effortlessly import approved pack content into Adobe illustrator. They can easily access verified information directly within the illustrator and incorporate it into the artwork layout. This streamlined approach minimizes the risk of manual errors during content integration and ensures that the final artwork aligns perfectly with approved specifications before proceeding to production.
Leveraging ManageArtworks artwork management tools at each stage of the packaging artwork lifecycle, can enhance efficiency, accuracy, and compliance, ultimately reducing the risk of errors and preventing costly product recalls. Book a free demo now to elevate your packaging artwork management game.